一文看懂芯片的封装工艺(先进封装篇2:晶圆级封装)
日期:2025-05-08 14:58:22 / 人气:34
"今天继续讲先进封装。
晶圆级封装
我们看下一个先进封装的关键概念——晶圆级封装(Wafer Level Package,WLP)。
传统封装,是先切割晶圆,再封装。
而晶圆级封装的核心逻辑,是在晶圆上直接进行封装,然后再切割,变成芯片。
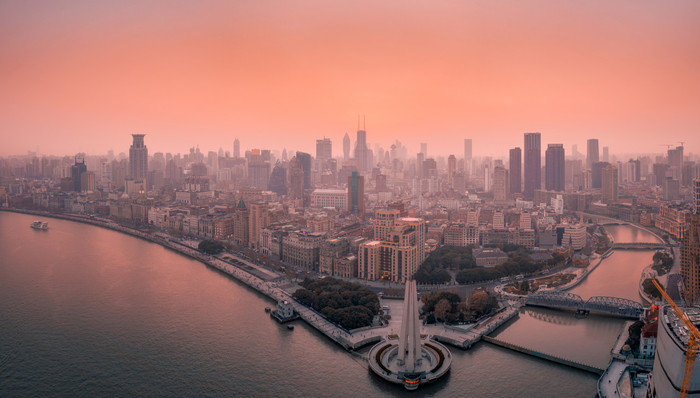
举个例子:传统封装,是先把大面团切成一块块,然后分别烘烤成蛋糕,分给大家吃。而晶圆级封装,是先烤一个大蛋糕,然后切成一块块,分给大家吃。
从更广泛的意义上讲,任何在晶圆这一层级进行全部或部分加工的封装,都可以被认为是晶圆级封装。
晶圆级封装出现于2000年左右,是半导体产业追求更高效率、更低成本的产物。
在晶圆上进行封装过程,能够带来以下好处:
1、由于侧面未涂覆封装材料,因此封装后的芯片尺寸较小。晶圆上,晶粒的密度更高,平均成本更低。
2、方便批量生产制造芯片,缩短工期,总体成本也比较低。
3、芯片设计和封装设计可以统一考虑,提升设计效率,降低设计成本。
晶圆级封装,可以分为:扇入型晶圆级封装(Fan-In WLP)和扇出型晶圆级封装(Fan-Out WLP)。
这里的“扇(Fan)”,指的是芯片的尺寸。
我们分别来介绍。
扇入型WLP(FIWLP)
早期的WLP,多采用扇入型。扇入型的封装布线、绝缘层以及锡球,都位于晶圆的顶部。封装后的尺寸,和芯片尺寸是相同的。
上期小枣君说过,芯片面积与封装面积之比超过1:1.14的封装,是CSP(芯片级封装)。扇入型WLP都1:1了,显然也属于CSP。所以,由扇入型晶圆级封装技术制成的封装,也称为晶圆级芯片级封装(WLCSP)。
扇入型WLP,通常可以分为BOP(Bump On Pad,垫上凸点)和RDL(ReDistribution Layer,重布线层)两种方式。
BOP封装的结构非常简单,Bump(凸点)直接构建在Al pad(铝衬板)的上面。如果Bump的位置远离Al pad,那么,就需要通过借助RDL技术,将Bump与Al pad进行连接。
大名鼎鼎的RDL,终于出现了。
我们需要单开一节,专门介绍一下它。
RDL
RDL的全称,是ReDistribution Layer(重布线层)。
RDL是晶圆级封装(WLP)的核心技术,也是后面2.5D/3D立体封装的核心技术。在先进封装里,它占有重要地位。
它是在晶粒下面的中介层上进行重新布线,实现I/O端口的重新布局。
简单来说,它就像我们平时看到的PCB电路板。只不过,真正的PCB板是在芯片的外面,把各个成品芯片和元器件连起来。
而RDL,是封装内部的“PCB板”,方便了XY平面(横向平面)的电气延伸和互联。它提升了封装内部电气连接的灵活性,能够让芯片内部布局更合理、更紧凑。
基于RDL,晶圆芯片上的“细间距”外围阵列,可以变成“更大间距”阵列。
基于之前晶圆制造的文章,大家会发现,RDL很像晶粒内部的金属连线(立交桥)。
晶粒内的金属沉积
是的,RDL的工艺,和晶圆制作流程中的“盖楼”流程差不多(可以参考晶圆制作的那期),主要就是光刻、涂胶显影、刻蚀、溅射沉积、电镀铜等工艺。
RDL也属于将晶圆制造(前道)工艺降维到封装(后道)中使用。和凸点一样,也是中道工序。
目前,主流的RDL工艺有两种:
第一种,是基于感光高分子聚合物,并结合电镀铜与刻蚀工艺实现。
1、 在晶圆表面涂覆一层聚合物薄膜,可选的聚合物材料包括光敏聚酰亚胺(PI)、苯并环丁烯(BCB)以及聚苯并恶唑(PBO)。这是为了增强芯片的钝化层并起到应力缓冲的作用。
2、加热固化后,使用光刻工艺在所需位置进行开孔,之后进行刻蚀。
3、通过物理气相沉积工艺(PVD),溅射Ti(钛)与Cu(铜),分别作为阻挡层与种子层。
4、再来一波光刻、刻蚀工艺,把RDL层的空间给挖出来。
5、通过电镀Cu工艺,在暴露出的Ti/Cu层上制造第一层RDL。(注意,电镀是将电解质溶液中的金属离子还原为金属并沉积在晶圆表面。)
6、去除掉光刻胶,并刻蚀掉多余的Ti/Cu。
7、涂覆第二层聚合物薄膜,使圆片表面平坦化并保护RDL层。
8、重复上述步骤,制作多层RDL结构。
另一种工艺,是采用Cu大马士革工艺结合PECVD与CMP工艺实现。
图我实在是不想画了,网上找了一个,供参考:
大致流程:
1、先采用PECVD工艺,沉积SiO2或Si3N4,作为绝缘层。
2、利用光刻与反应离子刻蚀,在绝缘层上形成窗口。
3、分别溅射Ti/Cu的阻挡/种子层以及导体铜,和刚才工艺一样。
4、采用CMP(化学机械研磨,之前介绍过的)工艺,将导体层减薄至所需厚度,形成了一层RDL或通孔层。
5、 重复上述步骤,制作多层RDL结构。
基于大马士革工艺制作的多层RDL内部构架
第二种工艺需要采用CMP,制造成本比第一种高。在行业里,第一种用得比较多。
制作完RDL之后,是制作UBM(凸点下金属层),工艺和RDL相似。
制作完UBM之后,通过掩膜板准确定位焊膏和焊料球,并将其放置于UBM上。
随后,进行回流,使焊料与UBM形成良好的浸润结合,从而确保达到理想的焊接效果。
综合以上步骤,扇入型WLP的大致工艺流程如下:
1、完成RDL布线,方便将I/O引出至方便焊接的位置。
2、对晶圆进行减薄加工。
3、在RDL层所连接的金属焊盘上,进行植球。
4、对晶圆进行切割,得到独立的芯片。
5、完成FT测试,出厂。
过去的20多年,扇入型WLP广泛应用于移动、便携式和消费类产品。特别是低I/O引脚数(≤200)、小芯片尺寸(≤ 6mm x 6 mm)、低成本、低端、薄型和大容量应用的半导体器件,使用这种封装比较多。
扇出型WLP(FOWLP)
扇入型WLP虽然面积小,但是支持的I/O引脚数也少。随着时间的推移,芯片的I/O引脚数逐渐增加,扇入型WLP无法满足要求。于是,就有了扇出型WLP(FOWLP)。
Fan-In WLP与Fan-Out WLP
扇出型WLP中,RDL可以向外延伸布线。这样一来,封装的面积大于晶粒的面积,I/O引脚数可以更多,引脚间距也宽松。
扇出型WLP如果符合CSP的尺寸比例要求,就是扇出型WLCSP。
扇出型WLP最早于2006年由英飞凌最先提出。他们在手机基带芯片封装中实现了量产,并将其命名为嵌入式晶圆级球栅阵列(eWLB)。
后来,扇出型WLP并没有获得什么关注。
直到2016年,台积电基于FOWLP,推出了集成扇出型(InFO)封装,并成功应用于苹果公司iPhone 7系列手机的A10处理器(AP)中,才让扇出型WLP获得了整个行业的高度关注。
凭借该项技术,台积电成功包揽了苹果公司之后每一代手机的AP芯片制造和封装订单。
后来,FOWLP高速发展,衍生出多种变体,包括核心扇出(Core FO)、高密度扇出(High-Density FO)和超高密度扇出(Ultra High Density FO)等,可以应用于不同的需求场景。
我们来看看FOWLP的工艺过程。
前面说WLP是先封装,再切割。这句话其实不太适用于FOWLP。
FOWLP,是先切割,然后把芯片重新放置在人工载板上。接下来,再进行晶圆级封装。封装完,再次切割,变成最终的芯片。
Fan-Out WLCSP工艺流程
根据工艺过程,扇出式WLP可以分为芯片先装(Die First)和芯片后装(Die Last)。芯片先装又分为面朝下(Face Down)、面朝上(Face Up)。
芯片先装,简单地说,就是先把芯片放上, 再做布线(RDL)。
芯片后装,就是先做布线(RDL)。测试合格的单元,再把芯片放上去。
芯片后装的优点,是可以提高合格芯片的利用率,以此提高成品率,降低成本。也有缺点,就是工艺相对复杂。
总结一下FOWLP的优点:
1、FOWLP是一种无载板(Substrate-less)的封装方式,不需要封装载板,更不用引线,可以大幅降低成本。
2、FOWLP没有封装载板,所以垂直高度更低,能够提供额外的垂直空间,向上堆叠更多的元件。
3、FOWLP厚度较薄,缩短芯片与散热片之间的距离,有利于散热。
4、FOWLP可以将不同功能的芯片进行灵活集成,进而完成系统级封装(SiP)。这是后摩尔时代非常重要的技术手段之一。
扇出面板级封装(FOPLP)
提到FOWLP,就肯定要提一下最近几年特别火的FOPLP。
FOPLP(扇出面板级封装),是扇出型封装的一种,也基于重新布线层(RDL)工艺。
它和 FOWLP非常类似,最大的区别在于:FOPLP使用的载板,不是 8寸/12寸的晶圆,而是方形的大尺寸面板。
FOPLP具有以下优势:
1、低成本。
FOPLP采用方形的大尺寸面板,不仅单片产出的芯片数量更多,而且面积利用率更高。根据 国际权威研究机构Yole的数据, FOWLP技术面积使用率<85%,而FOPLP技术面积使用率>95%。
以600mmX600mm尺寸的面板为例,面积为12寸wafer carrier的5.1倍,单片产出数量大幅提升。
FOPLP可以 大幅提高材料利用率和生产效率,进而降低生产成本。
例如,FOWLP采用旋转涂布工艺,PI、PR等光敏材料(价格昂贵)的有效利用率只有20%。FOPLP采用狭缝涂布工艺,材料有效利用率达到85%以上。
2、高灵活性。
FOPLP的生产灵活性更高,适合大批量生产,生产周期更短。
例如,FOWLP封装中,光罩的尺寸小,单次曝光面积有上限,需要通过拼接的方式曝光,效率低,良率低,影响产能。
而FOPLP封装,单次曝光面积是FOWLP的4倍以上,效率高、良率高,大幅提升了产能。
3、 优秀的热管理。
通过优化封装结构,以及选择合适的材料,FOPLP可以有更好的散热性能,降低芯片工作温度,提高芯片的可靠性和寿命。
4、高集成度。
FOPLP在大面板上重新分布半导体芯片,能够在单个封装内集成多个芯片、无源元件和连接,可以实现更高的集成度,甚至更高的性能。
集成更多功能模块,可以减少封装步骤和材料消耗,也能降低成本。
5、高电气性能。
FOPLP具有更低的电感和电容效应,电气性能出色。
图片来自亚智科技
当然,FOPLP也有缺点,包括 面板尺寸和组装工艺未能标准化、封装密度较低 ( 与FOWLP相比),以及芯片翘曲问题等。
目前, FOPLP板级封装凭借刚才提到的优点,在射频芯片、电源芯片、高频芯片、传感器芯片等领域展现了非常不错的应用前景。
包括台积电、英伟达、三星、 群创光电等在内的很多厂商,都表示了对FOPLP的关注,也投入了大量的资源。FOPLP的市场份额在不断攀升,预计2027年左右会进入一个技术成熟阶段,应用于AI GPU等芯片封装场景。
另外值得一提的,是FOPLP所使用的玻璃载板材料。
FOPLP载板的面积大,所以,在生产和处理的过程中,容易出现翘曲等问题。
所以,相比于传统的硅材料,FOPLP的载板材料主要是金属、玻璃或其它高分子聚合物材料。在这些材料之中,玻璃在机械、物理、光学等性能上具有明显的优势,现在已经成为行业关注的焦点。
玻璃基板的表面比塑料(有机材料)基板更光滑。在同样面积下,能够开孔(下期会提到的通孔)的数量也比塑料基板多。这极大提升了芯片之间的互连密度,有利于实现更复杂的设计,更有效地利用空间。
在热学性能、物理稳定度方面,玻璃基板也表现出色,不容易因为温度高而发生翘曲或变形。
玻璃基板的电气性能也突出,介电损耗更低,电气连接更稳定、高效。
目前,业界关于玻璃基板的研究和布局也同样激烈。
好了,关于晶圆级封装(WLP)的知识,就先介绍到这里。
下一期,是芯片封装专题的最后一期,我们讲讲2.5D/3D封装,还有背后非常重要的TSV/TGV、混合键合等技术。
参考文献:
1、《芯片制造全工艺流程》,半导体封装工程师之家;
2、《 半导体后端制造:传统封装和晶圆级封装》,Semika;
3、《 一文了解硅通孔(TSV)及玻璃通孔(TGV)技术》,圆圆de圆,半导体全解;
4、《 摩尔定律重要方向,先进封装大有可为》,华福证券 ;
5、《 FOPLP扇出型板级封装》, AshiRiga,知乎;
6、 《 一文看懂晶圆级封装》, skhynix官网,半导体行业观察;
7、《 一文了解载带自动焊接(TAB)技术 》,小陈婆婆,学习那些事;
8、 《 玻璃基板成为芯片封装竞争新热点》,东吴证券;
9、《 技术发展引领产业变革,向高密度封装时代迈进》,华金证券;
10、《 先进封装高密度互联推动键合技术发展,国产设备持续突破 》,东吴证券;
11、《 算力时代来临,Chiplet 先进封装大放异彩》,民生证券;
12、《 先进封装设备深度报告》,华西证券;
13、《 半导体封测行业深度报告》,华福证券;
14、《 深度分析半导体封装技术趋势,FOPLP前景如何?》,芯师爷;
15、《 技术前沿:面板级封装FOPLP》,ittbank;
16、《 先进封装技术-扇出型晶圆级封装(FOWLP)》,CAE工程师笔记;
17、维基百科、百度百科、各厂商官网。
"
晶圆级封装
我们看下一个先进封装的关键概念——晶圆级封装(Wafer Level Package,WLP)。
传统封装,是先切割晶圆,再封装。
而晶圆级封装的核心逻辑,是在晶圆上直接进行封装,然后再切割,变成芯片。
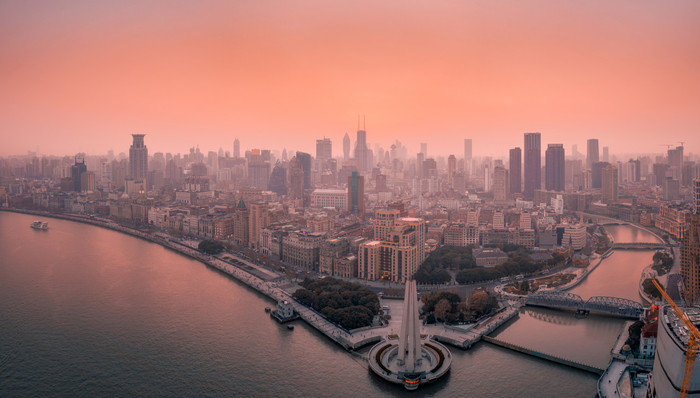
举个例子:传统封装,是先把大面团切成一块块,然后分别烘烤成蛋糕,分给大家吃。而晶圆级封装,是先烤一个大蛋糕,然后切成一块块,分给大家吃。
从更广泛的意义上讲,任何在晶圆这一层级进行全部或部分加工的封装,都可以被认为是晶圆级封装。
晶圆级封装出现于2000年左右,是半导体产业追求更高效率、更低成本的产物。
在晶圆上进行封装过程,能够带来以下好处:
1、由于侧面未涂覆封装材料,因此封装后的芯片尺寸较小。晶圆上,晶粒的密度更高,平均成本更低。
2、方便批量生产制造芯片,缩短工期,总体成本也比较低。
3、芯片设计和封装设计可以统一考虑,提升设计效率,降低设计成本。
晶圆级封装,可以分为:扇入型晶圆级封装(Fan-In WLP)和扇出型晶圆级封装(Fan-Out WLP)。
这里的“扇(Fan)”,指的是芯片的尺寸。
我们分别来介绍。
扇入型WLP(FIWLP)
早期的WLP,多采用扇入型。扇入型的封装布线、绝缘层以及锡球,都位于晶圆的顶部。封装后的尺寸,和芯片尺寸是相同的。
上期小枣君说过,芯片面积与封装面积之比超过1:1.14的封装,是CSP(芯片级封装)。扇入型WLP都1:1了,显然也属于CSP。所以,由扇入型晶圆级封装技术制成的封装,也称为晶圆级芯片级封装(WLCSP)。
扇入型WLP,通常可以分为BOP(Bump On Pad,垫上凸点)和RDL(ReDistribution Layer,重布线层)两种方式。
BOP封装的结构非常简单,Bump(凸点)直接构建在Al pad(铝衬板)的上面。如果Bump的位置远离Al pad,那么,就需要通过借助RDL技术,将Bump与Al pad进行连接。
大名鼎鼎的RDL,终于出现了。
我们需要单开一节,专门介绍一下它。
RDL
RDL的全称,是ReDistribution Layer(重布线层)。
RDL是晶圆级封装(WLP)的核心技术,也是后面2.5D/3D立体封装的核心技术。在先进封装里,它占有重要地位。
它是在晶粒下面的中介层上进行重新布线,实现I/O端口的重新布局。
简单来说,它就像我们平时看到的PCB电路板。只不过,真正的PCB板是在芯片的外面,把各个成品芯片和元器件连起来。
而RDL,是封装内部的“PCB板”,方便了XY平面(横向平面)的电气延伸和互联。它提升了封装内部电气连接的灵活性,能够让芯片内部布局更合理、更紧凑。
基于RDL,晶圆芯片上的“细间距”外围阵列,可以变成“更大间距”阵列。
基于之前晶圆制造的文章,大家会发现,RDL很像晶粒内部的金属连线(立交桥)。
晶粒内的金属沉积
是的,RDL的工艺,和晶圆制作流程中的“盖楼”流程差不多(可以参考晶圆制作的那期),主要就是光刻、涂胶显影、刻蚀、溅射沉积、电镀铜等工艺。
RDL也属于将晶圆制造(前道)工艺降维到封装(后道)中使用。和凸点一样,也是中道工序。
目前,主流的RDL工艺有两种:
第一种,是基于感光高分子聚合物,并结合电镀铜与刻蚀工艺实现。
1、 在晶圆表面涂覆一层聚合物薄膜,可选的聚合物材料包括光敏聚酰亚胺(PI)、苯并环丁烯(BCB)以及聚苯并恶唑(PBO)。这是为了增强芯片的钝化层并起到应力缓冲的作用。
2、加热固化后,使用光刻工艺在所需位置进行开孔,之后进行刻蚀。
3、通过物理气相沉积工艺(PVD),溅射Ti(钛)与Cu(铜),分别作为阻挡层与种子层。
4、再来一波光刻、刻蚀工艺,把RDL层的空间给挖出来。
5、通过电镀Cu工艺,在暴露出的Ti/Cu层上制造第一层RDL。(注意,电镀是将电解质溶液中的金属离子还原为金属并沉积在晶圆表面。)
6、去除掉光刻胶,并刻蚀掉多余的Ti/Cu。
7、涂覆第二层聚合物薄膜,使圆片表面平坦化并保护RDL层。
8、重复上述步骤,制作多层RDL结构。
另一种工艺,是采用Cu大马士革工艺结合PECVD与CMP工艺实现。
图我实在是不想画了,网上找了一个,供参考:
大致流程:
1、先采用PECVD工艺,沉积SiO2或Si3N4,作为绝缘层。
2、利用光刻与反应离子刻蚀,在绝缘层上形成窗口。
3、分别溅射Ti/Cu的阻挡/种子层以及导体铜,和刚才工艺一样。
4、采用CMP(化学机械研磨,之前介绍过的)工艺,将导体层减薄至所需厚度,形成了一层RDL或通孔层。
5、 重复上述步骤,制作多层RDL结构。
基于大马士革工艺制作的多层RDL内部构架
第二种工艺需要采用CMP,制造成本比第一种高。在行业里,第一种用得比较多。
制作完RDL之后,是制作UBM(凸点下金属层),工艺和RDL相似。
制作完UBM之后,通过掩膜板准确定位焊膏和焊料球,并将其放置于UBM上。
随后,进行回流,使焊料与UBM形成良好的浸润结合,从而确保达到理想的焊接效果。
综合以上步骤,扇入型WLP的大致工艺流程如下:
1、完成RDL布线,方便将I/O引出至方便焊接的位置。
2、对晶圆进行减薄加工。
3、在RDL层所连接的金属焊盘上,进行植球。
4、对晶圆进行切割,得到独立的芯片。
5、完成FT测试,出厂。
过去的20多年,扇入型WLP广泛应用于移动、便携式和消费类产品。特别是低I/O引脚数(≤200)、小芯片尺寸(≤ 6mm x 6 mm)、低成本、低端、薄型和大容量应用的半导体器件,使用这种封装比较多。
扇出型WLP(FOWLP)
扇入型WLP虽然面积小,但是支持的I/O引脚数也少。随着时间的推移,芯片的I/O引脚数逐渐增加,扇入型WLP无法满足要求。于是,就有了扇出型WLP(FOWLP)。
Fan-In WLP与Fan-Out WLP
扇出型WLP中,RDL可以向外延伸布线。这样一来,封装的面积大于晶粒的面积,I/O引脚数可以更多,引脚间距也宽松。
扇出型WLP如果符合CSP的尺寸比例要求,就是扇出型WLCSP。
扇出型WLP最早于2006年由英飞凌最先提出。他们在手机基带芯片封装中实现了量产,并将其命名为嵌入式晶圆级球栅阵列(eWLB)。
后来,扇出型WLP并没有获得什么关注。
直到2016年,台积电基于FOWLP,推出了集成扇出型(InFO)封装,并成功应用于苹果公司iPhone 7系列手机的A10处理器(AP)中,才让扇出型WLP获得了整个行业的高度关注。
凭借该项技术,台积电成功包揽了苹果公司之后每一代手机的AP芯片制造和封装订单。
后来,FOWLP高速发展,衍生出多种变体,包括核心扇出(Core FO)、高密度扇出(High-Density FO)和超高密度扇出(Ultra High Density FO)等,可以应用于不同的需求场景。
我们来看看FOWLP的工艺过程。
前面说WLP是先封装,再切割。这句话其实不太适用于FOWLP。
FOWLP,是先切割,然后把芯片重新放置在人工载板上。接下来,再进行晶圆级封装。封装完,再次切割,变成最终的芯片。
Fan-Out WLCSP工艺流程
根据工艺过程,扇出式WLP可以分为芯片先装(Die First)和芯片后装(Die Last)。芯片先装又分为面朝下(Face Down)、面朝上(Face Up)。
芯片先装,简单地说,就是先把芯片放上, 再做布线(RDL)。
芯片后装,就是先做布线(RDL)。测试合格的单元,再把芯片放上去。
芯片后装的优点,是可以提高合格芯片的利用率,以此提高成品率,降低成本。也有缺点,就是工艺相对复杂。
总结一下FOWLP的优点:
1、FOWLP是一种无载板(Substrate-less)的封装方式,不需要封装载板,更不用引线,可以大幅降低成本。
2、FOWLP没有封装载板,所以垂直高度更低,能够提供额外的垂直空间,向上堆叠更多的元件。
3、FOWLP厚度较薄,缩短芯片与散热片之间的距离,有利于散热。
4、FOWLP可以将不同功能的芯片进行灵活集成,进而完成系统级封装(SiP)。这是后摩尔时代非常重要的技术手段之一。
扇出面板级封装(FOPLP)
提到FOWLP,就肯定要提一下最近几年特别火的FOPLP。
FOPLP(扇出面板级封装),是扇出型封装的一种,也基于重新布线层(RDL)工艺。
它和 FOWLP非常类似,最大的区别在于:FOPLP使用的载板,不是 8寸/12寸的晶圆,而是方形的大尺寸面板。
FOPLP具有以下优势:
1、低成本。
FOPLP采用方形的大尺寸面板,不仅单片产出的芯片数量更多,而且面积利用率更高。根据 国际权威研究机构Yole的数据, FOWLP技术面积使用率<85%,而FOPLP技术面积使用率>95%。
以600mmX600mm尺寸的面板为例,面积为12寸wafer carrier的5.1倍,单片产出数量大幅提升。
FOPLP可以 大幅提高材料利用率和生产效率,进而降低生产成本。
例如,FOWLP采用旋转涂布工艺,PI、PR等光敏材料(价格昂贵)的有效利用率只有20%。FOPLP采用狭缝涂布工艺,材料有效利用率达到85%以上。
2、高灵活性。
FOPLP的生产灵活性更高,适合大批量生产,生产周期更短。
例如,FOWLP封装中,光罩的尺寸小,单次曝光面积有上限,需要通过拼接的方式曝光,效率低,良率低,影响产能。
而FOPLP封装,单次曝光面积是FOWLP的4倍以上,效率高、良率高,大幅提升了产能。
3、 优秀的热管理。
通过优化封装结构,以及选择合适的材料,FOPLP可以有更好的散热性能,降低芯片工作温度,提高芯片的可靠性和寿命。
4、高集成度。
FOPLP在大面板上重新分布半导体芯片,能够在单个封装内集成多个芯片、无源元件和连接,可以实现更高的集成度,甚至更高的性能。
集成更多功能模块,可以减少封装步骤和材料消耗,也能降低成本。
5、高电气性能。
FOPLP具有更低的电感和电容效应,电气性能出色。
图片来自亚智科技
当然,FOPLP也有缺点,包括 面板尺寸和组装工艺未能标准化、封装密度较低 ( 与FOWLP相比),以及芯片翘曲问题等。
目前, FOPLP板级封装凭借刚才提到的优点,在射频芯片、电源芯片、高频芯片、传感器芯片等领域展现了非常不错的应用前景。
包括台积电、英伟达、三星、 群创光电等在内的很多厂商,都表示了对FOPLP的关注,也投入了大量的资源。FOPLP的市场份额在不断攀升,预计2027年左右会进入一个技术成熟阶段,应用于AI GPU等芯片封装场景。
另外值得一提的,是FOPLP所使用的玻璃载板材料。
FOPLP载板的面积大,所以,在生产和处理的过程中,容易出现翘曲等问题。
所以,相比于传统的硅材料,FOPLP的载板材料主要是金属、玻璃或其它高分子聚合物材料。在这些材料之中,玻璃在机械、物理、光学等性能上具有明显的优势,现在已经成为行业关注的焦点。
玻璃基板的表面比塑料(有机材料)基板更光滑。在同样面积下,能够开孔(下期会提到的通孔)的数量也比塑料基板多。这极大提升了芯片之间的互连密度,有利于实现更复杂的设计,更有效地利用空间。
在热学性能、物理稳定度方面,玻璃基板也表现出色,不容易因为温度高而发生翘曲或变形。
玻璃基板的电气性能也突出,介电损耗更低,电气连接更稳定、高效。
目前,业界关于玻璃基板的研究和布局也同样激烈。
好了,关于晶圆级封装(WLP)的知识,就先介绍到这里。
下一期,是芯片封装专题的最后一期,我们讲讲2.5D/3D封装,还有背后非常重要的TSV/TGV、混合键合等技术。
参考文献:
1、《芯片制造全工艺流程》,半导体封装工程师之家;
2、《 半导体后端制造:传统封装和晶圆级封装》,Semika;
3、《 一文了解硅通孔(TSV)及玻璃通孔(TGV)技术》,圆圆de圆,半导体全解;
4、《 摩尔定律重要方向,先进封装大有可为》,华福证券 ;
5、《 FOPLP扇出型板级封装》, AshiRiga,知乎;
6、 《 一文看懂晶圆级封装》, skhynix官网,半导体行业观察;
7、《 一文了解载带自动焊接(TAB)技术 》,小陈婆婆,学习那些事;
8、 《 玻璃基板成为芯片封装竞争新热点》,东吴证券;
9、《 技术发展引领产业变革,向高密度封装时代迈进》,华金证券;
10、《 先进封装高密度互联推动键合技术发展,国产设备持续突破 》,东吴证券;
11、《 算力时代来临,Chiplet 先进封装大放异彩》,民生证券;
12、《 先进封装设备深度报告》,华西证券;
13、《 半导体封测行业深度报告》,华福证券;
14、《 深度分析半导体封装技术趋势,FOPLP前景如何?》,芯师爷;
15、《 技术前沿:面板级封装FOPLP》,ittbank;
16、《 先进封装技术-扇出型晶圆级封装(FOWLP)》,CAE工程师笔记;
17、维基百科、百度百科、各厂商官网。
"
作者:盛煌娱乐
新闻资讯 News
- 新风口,广东“双子星”出手了:...08-26
- 特朗普贸易攻势下:印度强硬反击...08-26
- 00 后大厨,真能 “一饭封神”?08-26
- Databricks:700 亿融资引爆硅谷...08-26